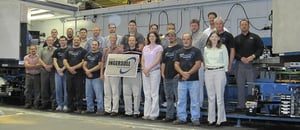
Crankshaft and Camshaft Machines
Our experts have mastered the crankshaft and camshaft machining process with our specialized machines and services.
Crankshaft and Camshaft Machines
We have more than 50 years of crankshaft and camshaft experience
.webp)
Crankshaft and Camshaft Machining Is What We Do Best
For nearly 50 years, Ingersoll CM Systems has designed and manufactured special machines for machining crankshafts and camshafts. It’s where we got our start. It’s what we do best. Our machines and services include deep fillet rolling, oil hole drilling, and cam lobe machining.
Deep Fillet Rolling
With the light-weighting of automobiles, every component of a vehicle has to be produced with the least amount of mass. This is true for crankshafts. Crankshafts are subject to high stresses and suffer from metal fatigue due to torsion and bending. Too, turbo-chargers on smaller engines produce higher horsepower and torque, thereby increasing metal fatigue.
By using deep fillet rolling, manufacturers can place high residual stresses into the under-cut corners of a crankshaft, thereby increasing the fatigue life of the unit.
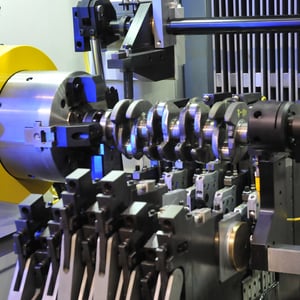
At Ingersoll, we offer a range of machines to provide deep fillet rolling. One of our most popular and most cost competitive versions is the DFR-600 machine. It is configurable for automobile crankshafts of 600 mm lengths to 800 mm lengths. Larger models are available for Diesel cranks up to 1300 mm in O.A.L.
- A full complement of rolling clamp arms that carry the rolling and support tools for crankshaft Main Journals and Pin Journals under-cuts.
- An optional Crankshaft Post Rolling tool set, when required. Each clamp arm uses a Gang-Hydraulic-Cylinder to provide rolling forces to 30 Kn [6,745 Lbf.] per Arm.
- Destructive and non-destructive fatigue tests are performed to validate the residual stress has been induced.
- Roller straightening is used with T.I.R. gage heads to assure the under-cuts do not wash-out in the grinding processes to follow the deep rolling.
Crankshaft Mill
Crankshaft castings and forgings are produced with stock material intentionally left in to be machined away. This assures the final product will be the exact shape and be properly balanced for high motor RPMs.
One of the initial machining processes of the crankshaft is to mill away the extra iron or steel of the pin journals and main journals.
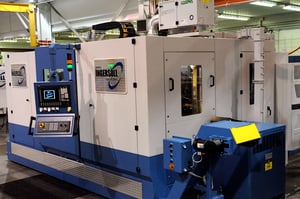
- EFM Features
- EFM Accessories
- EFM Options
The milling process generally removes 4 mm to 5 mm of material on radius, with a high material removal rate, using many cutting inserts engaged at a time. This often includes milling the side-walls and tops of the counterweight material. This provides clearance to the engine block, connecting rods, and piston skirts. Milling is normally done prior to the turning and grinding processes of the crankshafts, which remove much smaller amounts of stock.
Lathes can be used to remove this initial material too, but these take more production time than the milling process uses. To attain a TAKT time of 60 jobs per hour or higher, milling is the preferred process to remove the initial stock.
Ingersoll CM Systems offer crankshaft External Milling machines, EFM-800 or EFM-1300, that use fulcrums to pivot the large milling cutter into the crankshaft stock removal.
Most other manufacturer’s crankshaft mills use slides and are subject to high wear due to the milling impact and vibration. Fulcrums use large diameter pre-loaded roller bearings that can withstand the impact and vibration of the milling processes better than a slide.
The fulcrum is also driven in its pivoting motion by a preloaded roller-screw which is stronger and takes heavy loading better than a ball-screw. With this robust roller screw drive and preloaded Fulcrum bearings these machines can produce superior roundness to the milled journals. That can reduce the subsequent grinding time.
Crankshaft Mill
Description. Lorem ipsum dolor sit amet, consetetur sadipscing elitr, sed diam nonumy eirmod tempor invidunt ut labore et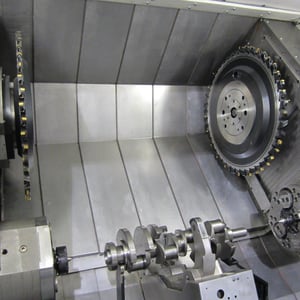
CNC Oil Hole Drill
Crankshafts in an engine need forced oil lubrication for the journal surfaces and the pin-journal surfaces inside the connecting rods. The lubrication delivery is provided by an oil pump in the engine and porting holes from the engine block bearings which pass through the crankshaft cross holes to the connecting rod. These oil holes in the crankshaft need to be produced accurately to assure they lubricate in the correct locations and do not weaken the crankshaft in the zones where it is subject to metal fatigue.
Crankshaft manufacturers need to use a very accurate CNC Oil Hole Drill that can produce these lubrication passages.
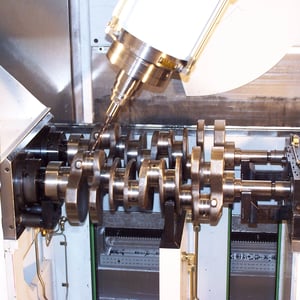
Description. Lorem ipsum dolor sit amet, consetetur sadipscing elitr, sed diam nonumy eirmod tempor invidunt ut labore et
Ingersoll CM Systems offers a patented design for a highly accurate oil hole drilling machine, AOHD-1050.
- The “A” stands for Agility due to the ease of changing this machine design over to a different crankshaft.
- The 1050 stands for the crankshaft length capacity of the fixtures.
This machine uses a special design to roll the oil hole drill centerline about the centerline of the crankshafts. Then, it only needs to feed the drill in one slide direction (Z-axis), without any interpolation, to produce the angled holes. This eliminates any 2-axis interpolation inaccuracies.
The machine control can be supplied with either a Siemens 840D-SL CNC or a Fanuc 31i CNC, depending on the manufacturer’s needs.
With the drill rotated around the crankshaft’s centerline, the entrance and exit of the holes location is accurate whether the crankshaft is 200 mm long or 1050 mm long, as compared to a machine using a regular rotary table under the fixture.
Turning
Description. Lorem ipsum dolor sit amet, consetetur sadipscing elitr, sed diam nonumy eirmod tempor invidunt ut labore et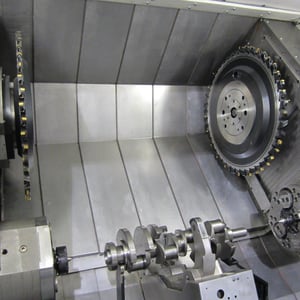
Cam Lobe Machine (CLM) Series
Camshaft manufacturers who produce their product from steel billet commonly use a form of contour cam lobe milling. Milling helps to achieve a near-net lobe profile for surface hardening, final grinding, and polishing. Full depth creep-feed grinding is too time consuming and wastes valuable grinding abrasive perishables to achieve this same near-net profile.
.webp?width=300&name=CLM%20Series%20Cam%20Lobe%20Mill%20(5).webp)
When in high production of cam lobes, a milling cutter with multiple effective cutting inserts is much more desirable. That is where the Ingersoll CM Systems CLM Series comes in. This single cutter-headed mill is both productive and very cost competitive in today’s market.
- It employs a 400 mm [15-3/4”] diameter, high density, milling cutter.
- The CLM is designed with a quick-change cutter ring with a stationary spindle adapter. With a non-planar cutter profile, you can achieve both long tool-life as well as re-entrant curvature on the lobe profile flanks. This provides distinct advantages over the use of an end-milling manufacturing method.
- Cam type change-over is made simple with chuck-jaw removal, center and radial-locator as a single cartridge design, NC movable tailstock, and easily positioning steady-rests with built-in “centering” journal diameter range.
This cam lobe mill is also available in a 1500 mm [59”] version with a double end synchronized drive.
- Rugged, compact milling machine.
- Exceptional positioning accuracy.
- Full S axis contouring and positioning.
- Highly flexible for various part types
- Fast work part change-over
- Single cutting head (S)
- Heavy-duty box way (X) / (Z)
- Long life screw for cutter motion
- User friendly operation & diagnostics
- CNC or fixed-position steady rest
- Totally enclosed guarding for chip and smoke/dust containment
- Single, robust, CNC programmable (S-axis), 10 – 200 rpm, cutting wheel.
- Box ways: heavy-duty, cast-iron, slide construction on X, Z, and optional W-axes.
- X-axis: Zero-backlash roller screw for stiffness and rigidity to accurately contour lobes and extend tool life.
- 100 – 1000 mm part length work envelope standard on model CLM-1000. 100 – 1500 mm envelope standard on CLM-1500. (Note: Longer work envelopes can be built.)
- Steady-rest support of journal diameters.
- Three-jaw, self-centering, 8” chuck at headstock (left) end of part. Optional, 6” chuck at tailstock (right) end. Chuck (C1 and C2-axes) angular positions are servo controlled. (Note: Left (C1-axis) and optional, right (C2-axis) chucks are electronically synchronized when machining to remove part torsion error during the cut.)
- Tailstock part-length encoder (standard, without optional W-axis).
- Enables tailstock coarse position control (±1.000 mm (±0.043”)) and part length monitoring. It uses the ‘Part Length’ value from the ‘Setup’ recipe screen for its approach and clamp positions. This eliminates manual tailstock assembly adjustments for parts that are about (100 mm (4”)) the same length, thereby simplifying changeover adjustments.
- Tailstock servo position control (with optional W-axis)
- Enables tailstock fine position control (±0.001 mm (±0.00025”)) and monitoring. It also uses the ‘Part Length’ value from the ‘Setup’ recipe screen for its approach and clamp positions. This eliminates manual tailstock assembly adjustments for ALL part changeovers.
- Latest Fanuc 0i-TF, CNC controller with FLadder PLC programming and memory storage for 35 part and 70 lobe types.
- Broken spindle belt detection.
- Part length detection (tailstock transducer).
- M-code individual or group control of steady-rests.
- Optional C2-axis (tailstock chuck) drive assist system.
- Optional Fanuc robot load/unload.
- Optional automatic loader door.
- Optional Fanuc Fast Connect network.
Here’s What Ingersoll CM Systems Customers Say
We Provide Custom CNC Machines to the World's Leading Manufacturers
Ingersoll CM Systems is a CNC partner to OEM, Tier 1 and Tier 2 suppliers in a wide range of industries.
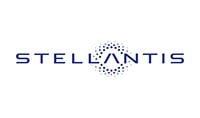
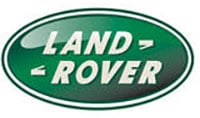

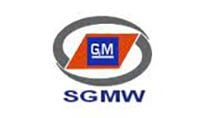
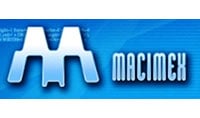
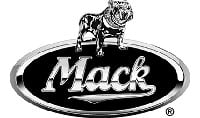
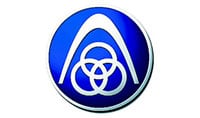
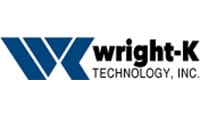
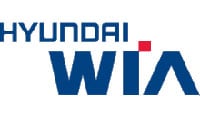
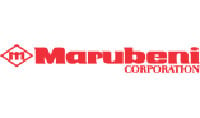
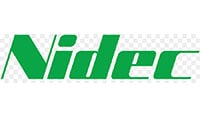
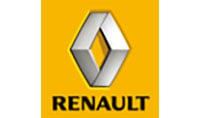
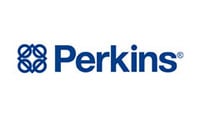
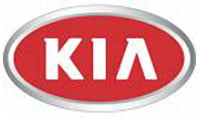
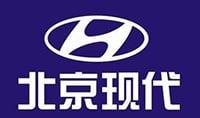
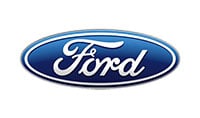
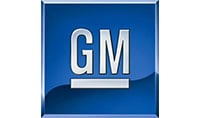
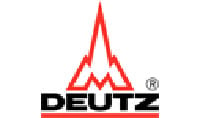
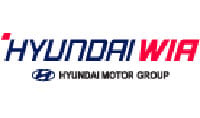
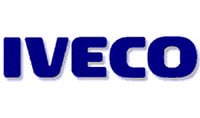
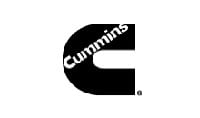
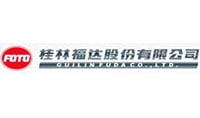
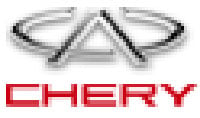
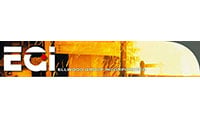
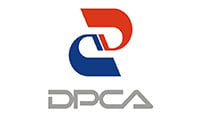
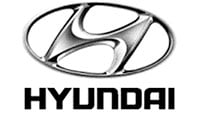
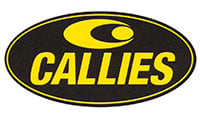
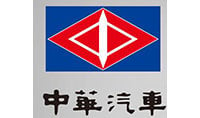
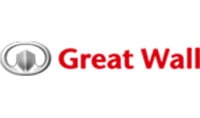
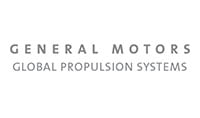
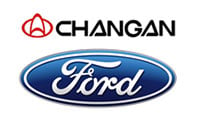
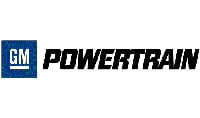
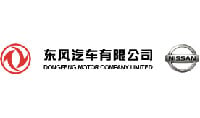
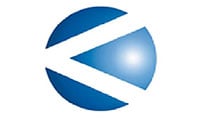
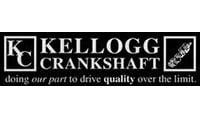
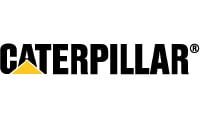
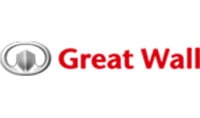
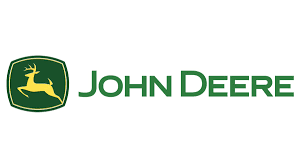
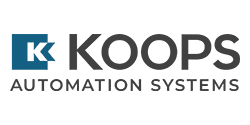
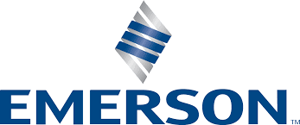
Need a Reliable Crankshaft Machine? Turn to Us as Your Solution.
Ingersoll CM Systems enjoys the business of repeat customers around the globe. Whether you need a new machine or to retool an existing machine, we can help. Give us a call at 989-495-5000 or click below to get started.